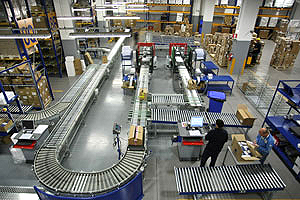
Si continua a parlare di material handling e di riduzione della spesa. In questa sede approfondiamo come l’organizzazione della movimentazione dei materiali in un’azienda possa portare a contenere (e in alcuni casi ridurre) i costi di gestione del magazzino: dai sistemi di picking all’organizzazione del magazzino, passando per il controllo delle scorte. Premessa Organizzazione, esecuzione e ottimizzazione della movimentazione materiali all'interno delle aziende, delle correnti di informazioni e del trasbordo di merci: ecco in cosa consiste l’intralogistica, un concetto che è stato delineato appunto per distinguersi da quello di logistica, di trasporto merci al di fuori di uno stabilimento. I mercati resi estremamente volatili dalla globalizzazione e la crescente complessità dei processi aziendali hanno fatto sì che l’intralogistica rispondesse ormai a esigenze sempre più sofisticate. Modularità, flessibilità, efficienza, funzionalità, disponibilità, economicità e sostenibilità: sono tutti valori fondamentali, tanto per le tecniche di stoccaggio e movimentazione quanto per i sistemi informatici e automatici di magazzino. Il magazzino non deve pertanto essere interpretato solamente come una entità fisica, ma piuttosto come un importante segmento della catena di fornitura, ed è condizionato e condiziona le strategie e le operazioni aziendali in termini di costi e servizio. L’impatto di questi costi logistici non è da sottovalutare, tanto più se questi hanno poi un riscontro sul costo di fabbricazione e produzione più in generale. Ottimizzare, dunque, non solo i parametri di gestione di un magazzino ma quelli di tutta la catena logistica può mettere in atto meccanismi di leva molto forti. Sistemi di picking Il picking è il prelievo degli articoli da un’area di stoccaggio intensivo allo scopo di soddisfare le richieste dei quantitativi di prodotti indicati negli ordini di spedizione o di lavorazione. Questa attività di prelievo risulta strettamente correlata all’attività successiva di smistamento delle unità prelevate ai diversi punti di raccolta o utilizzo. L’attività di picking ha acquistato un ruolo sempre più critico nell’ambito dei sistemi logistici, sia per quanto riguarda la logistica produttiva, sia per quanto riguarda la logistica distributiva. La rilevanza di una corretta progettazione del sistema di picking è legata alla criticità, in termini di costi e impatto sul livello di servizio (in termini di puntualità, flessibilità, accuratezza e completezza di consegna), che riveste in molti sistemi logistico-distributivi, e anche in taluni contesti produttivi. Data la criticità e rilevanza economica dell’attività di picking, spesso si dedica un’area separata del magazzino a tale attività. È bene precisare che sia nel caso si decida di progettare e organizzare un magazzino a partire da una situazione “green field”, sia nella fase di modifica o taratura delle logiche gestionali senza variare gli aspetti di configurazione del sistema, è necessario partire dall’analisi degli aspetti che aiutano nella definizione delle configurazione ottimale del sistema e delle sue logiche gestionali. L’analisi va svolta, generalmente, quando si osservano delle inefficienze nel sistema, tuttavia è consigliabile mantenere una certa sistematicità e periodicità, in modo che il sistema di picking sia sempre adattato al contesto mutevole. Il picking negli ultimi anni è diventata un’attività sempre più critica all’interno del magazzino. La sua importanza ha portato i fornitori di soluzioni di material handling a sviluppare sempre nuove soluzioni. Material handling, principi per ridurre le spese Considerando che il material handling è l’insieme delle operazioni che riguardano il trasporto, lo stoccaggio, il controllo e la protezione del materiale attraverso il processo di produzione, distribuzione ed esposizione dei prodotti industriali, diventa importante che tutti questi servizi siano previsti e pianificati allo scopo di minimizzare i costi complessivi. Soltanto in questo modo, infatti, è possibile apportare quei cambiamenti e quegli aggiustamenti capaci di migliorare in modo considerevole i costi di esercizio e l’efficienza del sistema, che sarebbero significativi dal punto di vista economico una volta costruito l’impianto. Anche il flusso dei materiali deve essere concepito come un unico sistema integrato, esteso dai fornitori fino ai clienti e agli utilizzatori in accordo con una visione più moderna della logistica industriale. Bisogna cercare di standardizzare non solo all’interno dei reparti produttivi e dei magazzini, ma anche nei confronti dei propri fornitori e degli utilizzatori. La riduzione e la razionalizzazione dei percorsi seguiti dai materiali hanno un grosso impatto tanto sui costi di movimentazione (sia di manodopera sia di impianto) quanto sugli aspetti della sicurezza, del controllo e del danneggiamento dei prodotti. La semplificazione delle operazioni è messa al primo posto: i materiali relativi a più prodotti, per esempio, non devono essere spostati in più viaggi, ma combinati in un’unica stazione di lavoro affinché si possano ridurre tempo e costi di trasferimento; quando è possibile, anche la configurazione impiantistica va modificata e adattata in modo da agevolare le operazioni. In materia di contenimento dei costi, lo stoccaggio deve seguire dei principi ben delineati: il materiale deve essere disposto andando a utilizzare tutto lo spazio a disposizione, sfruttando anche lo sviluppo verticale. Introdurre sistemi di movimentazione completamente automatizzati permette poi di ottenere una riduzione di manodopera con relativi costi, e soprattutto una sostituzione di mansioni poco gratificanti. Questa strumentazione deve poi essere periodicamente sottoposta a manutenzione, in modo tale da non dover ricorrere a controlli e riparazioni d’emergenza, in genere molto più costose. Di un sistema già funzionante vanno analizzati i metodi e le attrezzature, confrontandoli con i nuovi mezzi in commercio, magari più efficienti. Quando l’analisi costi-benefici lo rende conveniente, è opportuno sostituire le vecchie attrezzature con le nuove, migliorando così l’efficienza e le prestazioni del sistema. Il controllo, prima di tutto Il sistema di material handling è talmente rilevante per il successo di un centro distributivo che è possibile trarre conclusioni sull’impegno nell’organizzare il tutto per raggiungere l’eccellenza sulla base di come i materiali vengono immagazzinati, movimentati, controllati. Di questi tre aspetti, quello del controllo è di sicuro il meno visibile, ma è il più importante al fine di raggiungere le prestazioni auspicate. Attraverso sistemi di identificazione come il codice a barre, è possibile controllare l’ammontare delle giacenze di magazzino, arrivando sia a conoscere la disponibilità di prodotti sia ad avere allo stesso tempo la possibilità di intervenire qualora quella disponibilità scenda al di sotto dei livelli prefissati. Il modo in cui si esercita il controllo sui materiali attraverso l’intero centro distributivo influenza le future possibilità di automazione della movimentazione e dello stoccaggio dei materiali.